Monforts is introducing a range of modular upgrades that can be added to existing finishing lines already in production.
“Our machines are known for their robustness and long service life, but the retrofitting of specific modules with new control and drive technology – going far beyond the basic replacement of spare parts – can have a significant impact on the performance of an existing line,” says Monforts Marketing Manager Nicole Croonenbroek. “This is especially the case in achieving further energy savings. In today’s challenging times, Monforts is always a helpful and reliable partner to customers who may be considering switching their heating systems to other energy sources. Customers can contact us individually to check the possibilities that are available for their ranges.”
The Monforts universal Energy Tower– a flexible, free-standing air/air heat exchanger for recovering the heat from the exhaust air flow of thermal processes – can result in a 30% reduction in the energy consumed by a line, depending on the exhaust air volume and operating temperature.
A Monforts Eco Booster, completely integrated into the chamber design of the Montex stenter, is another retrofitting option. As a single state-of-the-art heat recovery system with automatic cleaning, it can be added to existing ranges. For ranges of up to eight chambers only one module is necessary to achieve significant energy savings.
On an eight-chamber stenter with an operating width of two metres carrying out a fixing process on a 150gsm woven fabric, for example, the energy savings have been calculated to be 35% over an annual schedule of 6,000 operating hours.
In addition, the Eco Booster consumes only minimal amounts of water during the cleaning cycle and the entire process is controlled and monitored automatically.
The Matex Eco Applicator is an alternative to the conventional padding process for energy-conscious finishing and achieving considerable savings in the energy required for drying treated fabrics. The precise amount of chemical can be applied to the fabric and with less residual moisture after application of only approximately 35% so that less drying capacity is required in the stenter, which leads to huge energy savings.
Finishes can be evenly applied on either or both sides of the fabric, and two separate treatments can be applied to front and back.
This makes the unit ideal for the production of, for example, double-performance hydrophobic/hydrophilic fabrics for professional clothing, as well as the over dyeing or finishing of denim fabrics.
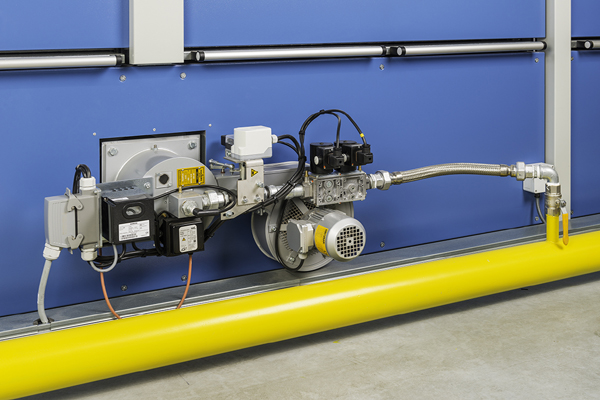
Options
“Other general retrofitting options available in our modular upgrade programme include a new clip opener for the stenter, which is located at the chain deflection points and reduces wear on the clip table and the blades,” says Achim Gesser, Monforts Head of Spare Parts. “At the same time, it ensures a quieter working atmosphere due to the smooth opening and closing of the clips. The addition of a glue flue selvedge dryer can meanwhile increase fabric transport speeds and improve fabric quality by protecting the fabric from overdrying.
“There are also considerable benefits to be gained from bringing a machine’s HMI up to date with our new 19-inch compact OS Windows 10 PCs, as well as with a range of frequency converter options for bringing a machine completely up to date technically and reducing downtimes.
“We’re happy to explain the range of modifications and modernisations that can be made to your line at any time. Compared to a new machine, upgrades are a low-cost investment that deliver clearly defined benefits. With more than 135 years of experience, Monforts is the right partner to assist valuable customers in offering retrofits to help with sustainability and energy savings.”
Further details of the Monforts modular upgrade programme are available at www.monforts.de/en/spare-parts-modifications/ or you can get in touch personally during Techtextil in Frankfurt from 21-24 June 2022, hall 12.0, booth B69.