Knopf’s Sohn, a leading contract finisher of technical textiles, has installed a fully automated Montex stenter at its plant in Helmbrechts, Germany.
The Montex machinery range is constantly being upgraded to meet evolving customer needs for greater automation, ease of operation and energy optimisation. The latest ten chamber line at Knopf’s Sohn, with a working width of up to 2.0 metres, was engineered to specific requirements in order to accelerate the company’s move to fully automatic control of its production, and high scaffolding was required for its installation.
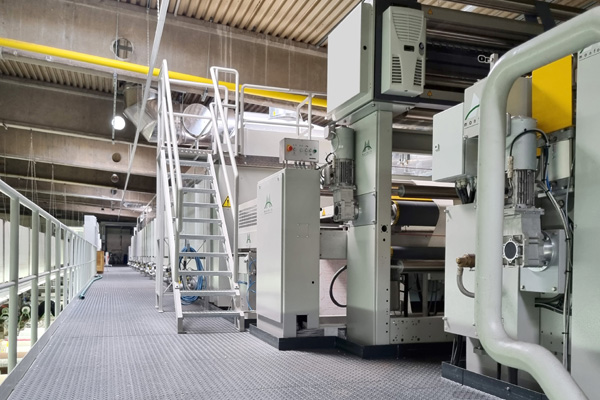
High scaffolding was required for the installation of the line which benefits from two integrated ECO Booster modules to provide significant energy savings.
The line benefits from two integrated ECO Booster modules to provide high energy savings. These compact, air-to-air heat exchangers, installed within the roof structure of the line, exploit energy from the exhaust gas to preheat up to 60% of the incoming fresh air entering the stenter.
The use of a single ECO Booster unit has been calculated to save up to 35% in energy costs, based on fixation processes. Fully automatic operation, set at the Monforts Qualitex control unit, ensures there is no additional burden on the machine operator.
The line is powered by Exxotherm indirect heating, which practically eliminates the yellowing which can be experienced during the treatment of certain polyamide and elastane-based fabrics, and is also equipped with a Conticlean circulating air filter system for constant high drying capacity, thanks to the automatic cleaning of fluff from the filter system during production.
Software
Knopf’s Sohn operates a total of five stenters, but the Montex takes automated finishing for the company to a new level.
The latest Qualitex visualisation software offers operators reliability and easy control with its full HD multi-touch monitor and slider function, dashboard function with individual adaptation to operating states and faster access to comprehensive recipe data management.
With the Monformatic control system, the exact maintenance of the dwell time in combined treatment processes (drying and heat-setting) can be monitored. When the heat-setting point is reached, the fan speed is automatically adjusted, keeping energy consumption fully under control
In general, Knopf’s Sohn is processing technical textiles for the automotive, aerospace, home furnishings and workwear markets, based on wool, cellulose, polyamide and polyester fabrics, along with elastane blends, in weights of 80-800gsm.
Founded in 1809 in a region well-known for textiles production, the company can draw on two centuries of accumulated know-how in all of the many processes. It is certified to ISO 9001, 14001 and 50001, as well as the bluesign standard for sustainable production.
“The ongoing success of our company is down to a combination of our many long-term, hardworking and loyal employees, loyal and innovative customers, and market and future-oriented business decisions,” said the company’s Managing Director Uwe Zuleg. “With the new Monforts Montex line we can now push ahead with our automation goals. The uniformity of the process temperature that can be achieved, as well as the overall concept of the line, convinced us to opt for this technology. From the first consultation to operator training, Monforts provided competent and service-oriented assistance, and delivery and installation remained on schedule despite the corona pandemic. The entire process was exemplary.”