Monforts and its Turkish representative Neotek are looking forward to meeting customers old and new at the forthcoming ITM 22 international textile machinery show which is taking place from June 14-18 at the Tüyap Fair and Congress Centre in Istanbul, after a three-year break.
“We will be emphasising the robustness and versatility of the Montex stenter for essential processes such as drying, stretching, heatsetting and coating at the Istanbul show,” said Monforts Area Sales Manager Thomas Päffgen. “The Montex has become the industry standard for the fabric finishing industry, providing a number of advantages in terms of production throughput and especially in energy efficiency and savings.”
“With energy prices rising steeply everywhere, features such as the MonforClean system, or the EcoBooster, in which waste heat from the drying process is used to pre-heat the drying air, are proving more invaluable than ever,” added Ahmet Kilic of Neotek. “Monforts can provide a range of further resource-saving and energy recovery options tailored to each individual line installation. We expect fruitful discussions on how we can meet the needs of our many mill partners during this key Istanbul event.”
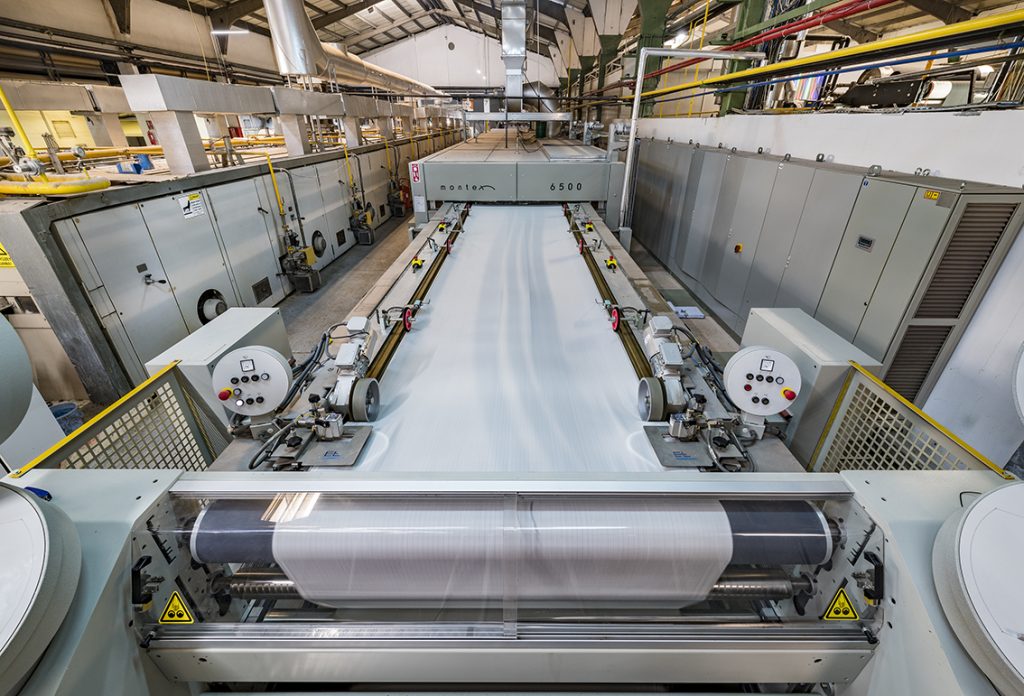
With the TwinAir heating chamber system within a Montex stenter, top and bottom airflows can be regulated completely independently of each other, ensuring heat is only applied when and where it is required. The Optiscan balancing system ensures continuous automatic evaluation of the distance between the nozzles and the fabric for highly economical and contact-free drying. The resulting constant evaporation rate within the stenter ensures optimum energy utilisation and also avoids markings on the fabric.
With the latest Montex stenters, overall energy savings of up to 40% can now be achieved compared to a conventional stenter with no heat recovery or energy optimisation measures like high-quality chamber insulation.
The Montex stenter also benefits from full digital control, with the Qualitex 800 PLC control system providing ease of operation and rapid access to line and management data, including full operating cost overviews, as well as maintenance monitoring.
Advances in digital technology mean that there are also now significant gains to be made in the retrofitting of existing Monforts machines with the latest automatic drives and control systems, going far beyond the basic replacement of spare parts.
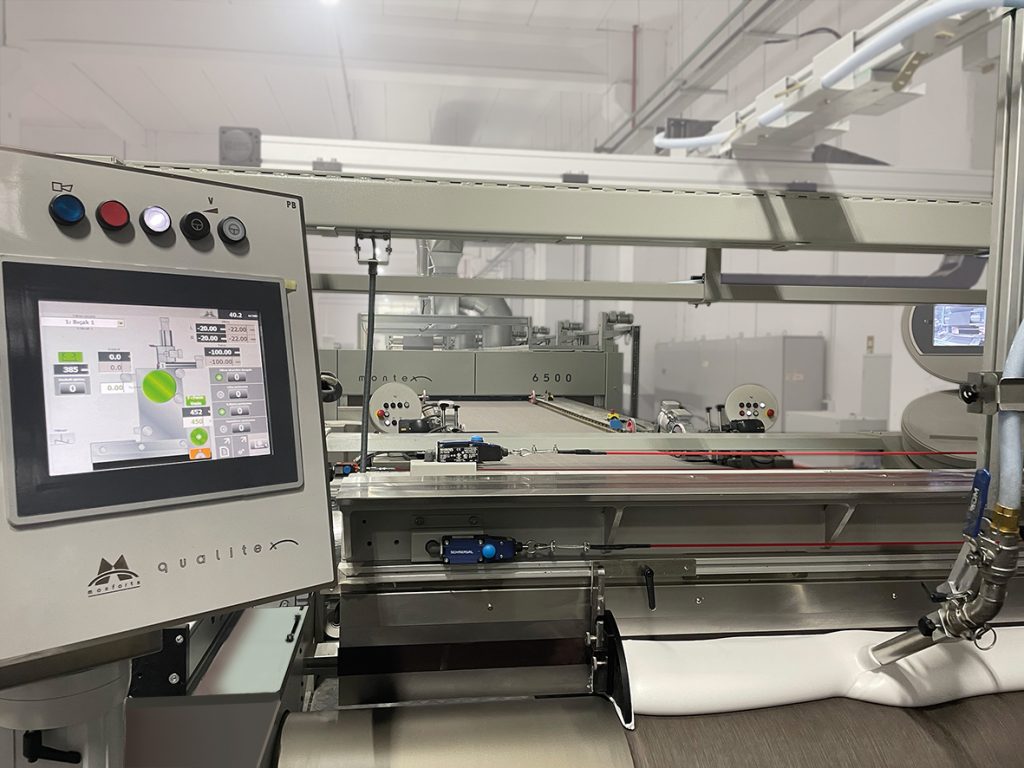
“We will be very happy to welcome you on our booth 1209B in hall 12 during ITM,” said Ahmet Kilic and Thomas Päffgen.